Stress-Strain curve of metal-polymer interface
Introduction
The mechanical properties of materials are important in a wide range of industries, including aerospace, automotive, and electronics. Metal-polymer composites, which are used in various applications such as electronic components, require robust metal-polymer bonding techniques. However, there are significant challenges in the microscopic evaluation of the mechanical phenomena at the interface.
Molecular Dynamics (MD) simulations can be used to evaluate the detailed mechanical properties of the metal-polymer composite interface. In addition, the elucidation of its microscopic behavior can be a powerful tool in the research and development of composite materials. However, traditional classical MD simulations have faced difficulties in generating accurate force fields for metal-polymer interfaces.
Matlantis, with its high versatility, is able to calculate metal-polymer interface with high accuracy. In this case study, we perform MD simulations on a composite structure of an iron slab and a thermoplastic resin (PEO) to evaluate its mechanical properties.
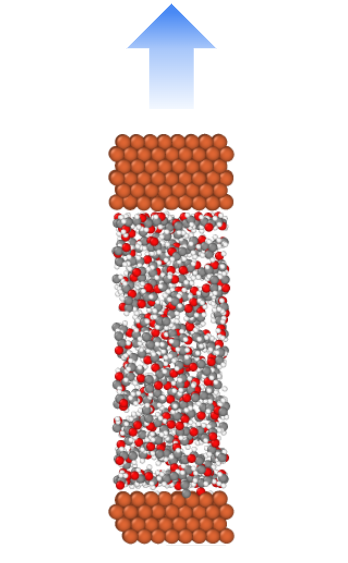
Computational Details
The slab structure was built using the Atomic Simulation Environment. The configuration of the polymer molecules was generated from SMILES using RDKit. The polymer molecules were inserted into the vacuum layer between the metal slabs. Then, the interface structure was compressed by applying a pressure of 1000 atm. The stress-strain curve was calculated by applying tensile strain along c-axis.
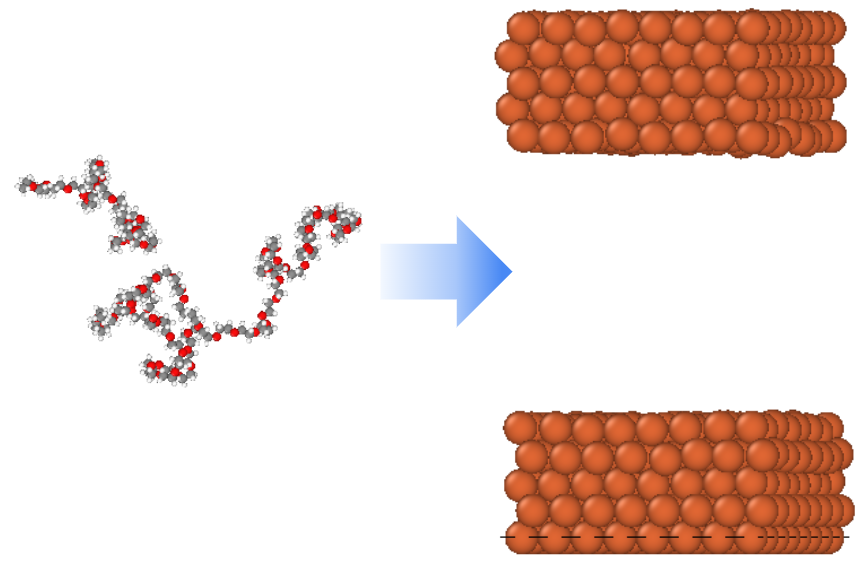
Results and Discussion
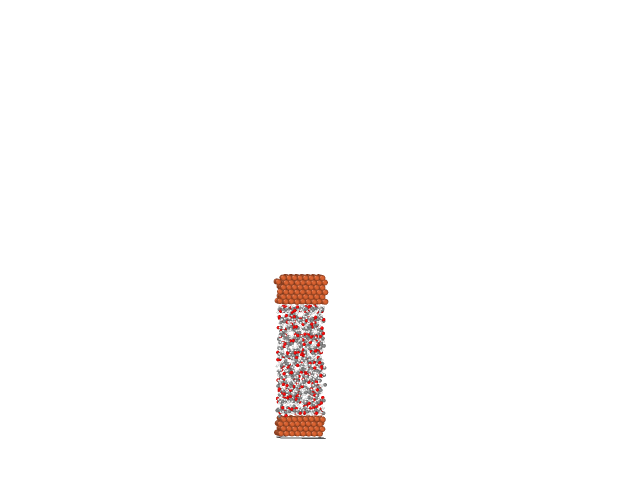
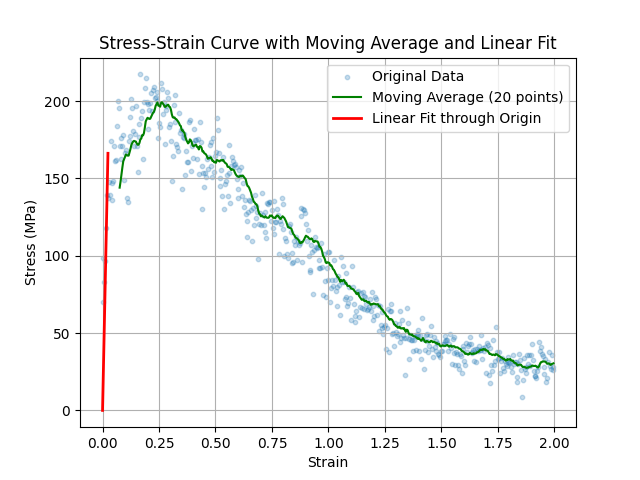
A moving average of the stress as a function of the applied strain yielded the stress-strain curve, which represents the mechanical strength of the material.
The Young’s modulus of 6.95GPa was obtained by linearly fitting the small strain region of the SS curve. At large strain, non-linear behavior was observed in the SS curve. A yield point was observed at a strain of 0.25, and the tensile strength was about 200MPa. The stress gradually decreased with strain above 0.25. The stress-strain curve obtained from the simulations is consistent with the characteristics commonly observed in resin materials.
This result demonstrates that MD simulations with Matlantis can be used to evaluate the mechanical strength of metal-polymer composite interfaces.
Computational conditions
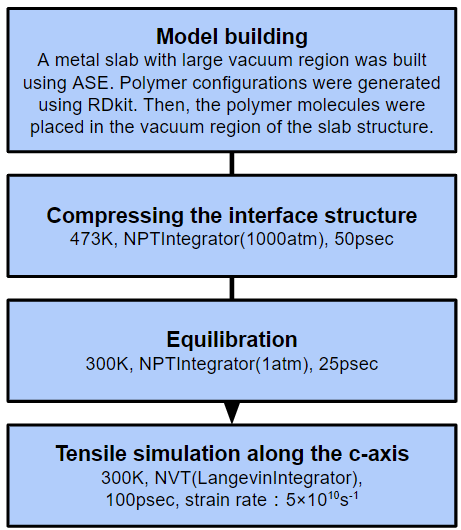
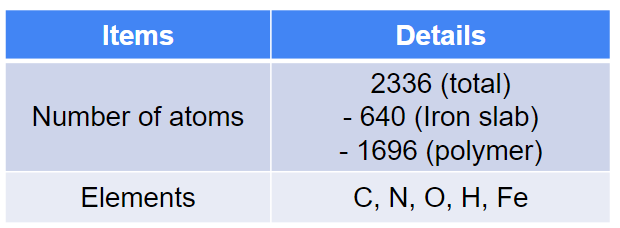